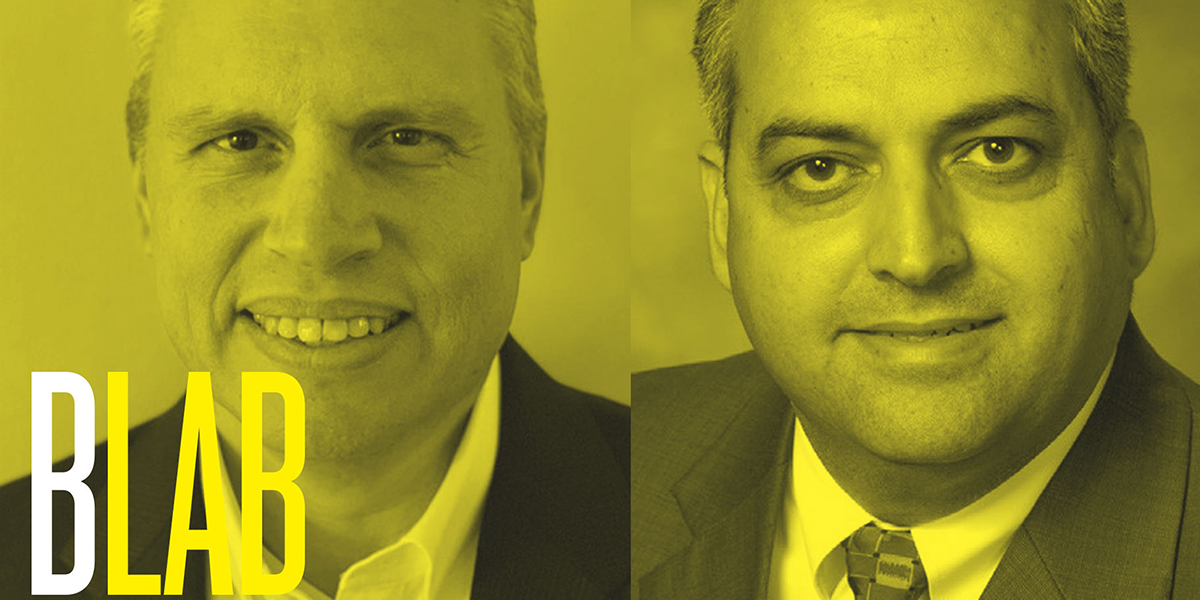
From cars to planes, the future of transportation is already here—and is changing rapidly. Software engineering is increasingly central to both the development and maintenance of all kinds of vehicles. That means more people need to start thinking like systems engineers. Dale Tutt, vice president of aerospace and defense industry for Siemens Software, says this means companies must offer more training and planning for those designing and developing vehicles of the future.
“As you try to address the talent gap, there’s a lot you can do to help make the tools easier to use. By better integrating the tools and by bringing in technologies like AI to help automate the generation of different design concepts and the analysis of those concepts using simulation tools, you can extend the capabilities of the system so that it helps empower your engineers,” says Tutt.
“Companies that are the most successful at adopting systems engineering are doing it because systems engineering, and the tools being used are becoming almost like the DNA of their engineering organization. Everyone is starting to think a bit like a systems engineer, even in their normal job. The tools and the ecosystem that you use to do systems engineering has a large role in facilitating adoption.”
Nand Kochhar, the vice president of automotive and transportation for Siemens Software, says a systems engineering approach can extend more broadly, as engineers think about how cars and vehicles connect to everything else in their environments.
“In a smart city, the system has become the city itself. Take a vehicle in the city, for example. The definition of the system has moved from the single vehicle to include the flow of traffic in the city and to how the traffic lights operate. You can extend that expansive ecosystem to other aspects like building management, for example, into the smart city environment,” he says.
“It becomes a totally different business case than what we have today. These new technologies are furthering innovation, both at the technical level as well as at a business model level. So, as a result of autonomy and the autonomous vehicle deployment, new business models are being formed.”
Full transcript
Laurel Ruma: From MIT Technology Review. I’m Laurel Ruma, and this is Business Lab, the show that helps business leaders make sense of new technologies coming out of the lab and into the marketplace.
Our topic today is the software-driven engineering environment. How a car or a plane is built now is much different than in the days of Henry Ford and the Wright Brothers. Vehicles and planes now have more software than hardware. As innovation evolves, the complexity of the software evolves as well, which allows for new types of inventions.
Two words for you: systems engineering.
My guests today are Nand Kochhar and Dale Tutt. Nand is the vice president of automotive and transportation for Siemens Software. He joined Siemens in 2020 after almost 30 years at Ford Motor Company, where he held a number of positions, including global safety systems chief engineer, and executive technical lead.
Dale Tutt is the vice president of aerospace and defense industry for Siemens Software. Prior to this role, Dale worked at The Spaceship Company. And in December 2018, he led the team on a successful flight to space. Welcome Nand and Dale.
Nand Kochhar: Thank you, Laurel.
Dale Tutt: Thank you, Laurel, we’re very excited to be here today.
Laurel: So, as product development across industries—including aerospace and defense, and automotive—transitions from mechanical engineering to a software-driven engineering environment, systems are growing in complexity. Software-driven engineering has given rise to the interdisciplinary field of systems engineering. In what way has this new field or new approach affected the industry as a whole—and aerospace and defense, and automotive, in particular?
Nand: This field has provided an opportunity for the automotive industry to continue to innovate. As you know, the trends in the industry are changing—we’re moving from internal combustion engines to new propulsion systems, going toward electrification. Our vehicles are also adapting to levels of autonomy, from SAE Level 1 to 5.
All that brings a lot of complexity. In fact, you could say software is eating the car, as software is becoming a predominant part of today’s automobile and future automobile development. The software engineering-based discipline has allowed us to address that growing complexity, and it has allowed our engineers to continue to innovate and offer products the end customer wants. That is the big change—how the product development and manufacturing in the automobile industry is changing.
Dale: As Nand was saying about the automotive industry, we’re seeing a need to innovate much more than we have in the past within aerospace and defense. Whether it’s building new air taxis or the EVTOL aircraft, the advances in space systems and putting more and more people into we’re changing the way we’re doing space exploration.
As we move into the future, the need for more sustainability and to address using less fuel and having greater efficiency in our systems has driven a lot innovation in the industry. Companies are using software to enable much more complex systems with the expectation that they’ll operate more efficiently, more effectively. In the case of aircraft, the expected result is a lower weight aircraft, which then uses less energy to go from one place to the next.
Systems engineering has been predominant in aerospace and defense for decades now. It’s now being used to help drive some of that innovation, to help make sure that we have looked at all of the possible combinations of a complex system, and possible failure modes of those systems, so that we can provide the safest, most reliable, highest-performing product possible for customers. So, while it’s been around for a long time, in looking at these complex systems, we’ve seen a tremendous growth in the need for systems engineering and model-based systems engineering among all of our customers to get the innovation they want to have.
Laurel: So, cars are evolving as are planes, and one could even say that there’s a massive shift, not just from combustion engines to electric vehicles, but also to autonomous vehicles for both of these great innovations. Nand, how does that affect cars in general and when we think about how systems are being used and changing so drastically?
Nand: Yes, as you said, it changes the entire product development approach when you look at autonomous vehicles or electric vehicles. So, let’s take one at a time. In electric vehicles, instead of having the combustion engines, of course, now, there is a battery system as the source of power generation. Then, you have the transmission of that power going through the wheels. So, a lot of the mechanisms in between are changing.
When we say it’s battery powered, to deliver electrification, it’s not just the battery. It is the entire electronics, which changes with it the whole architecture as well as the software. The software is performing what we call battery management because it’s continuously optimizing the operations of the battery so that it can deliver the power on demand and be the most efficient, while still addressing the cross-attribute issues of any thermal performance.
The fundamental shift is happening at a vehicle-attribute level, at a driver-vehicle performance level, and not only at the component level that you now have in rotors and motors and batteries, versus the previous systems. When you look at autonomy, it becomes even more complex, starting with the levels of autonomy to SAE Level 2, where you have both the braking functions as well as the steering functions and the decision-making happening. So, now you have an extra set of sensors in the car. They’re collecting information, collecting data all the time. That information is being sent to a central processing unit to make decisions, so you’ve got an extra set of software, the algorithms, making those decisions. Those decisions are going back into operations, whether it’s braking or whether it’s steering. So, the level of complexity has increased.
You can take it even further to the SAE Level 3 or 4. Now, you have the camera and LIDAR radar. Sensing systems also need to be talking to the infrastructure, whether that is the city traffic lighting or whether it is other parts of the transponders installed within the cities. The definition of the systems have changed. In the past, when we didn’t have advanced vehicles with levels of autonomy, the vehicle itself was called the system. It was a system of systems, and those subsystems were body, chassis, powertrain, electronics. Now, when you look at this autonomous environment, the vehicle itself has become a subsystem, and it is working in the system with other cars on the road and with the infrastructure, so the definition of systems have changed. This is how the approach of system of systems is the only way to address the kind of autonomy we want to enjoy down the road.
Laurel: Dale, with EVTOL, or electric vertical takeoff and landing aircrafts, just one example, is it similar in how the systems of systems are changing and evolving?
Dale: Absolutely. As Nand said, there was, for many years, a lot of focus on the aircraft or the product itself and thinking of it as a system of systems. With the use of drones, that became more of a system of systems problem, and the EVTOLs are a problem that’s very similar to what we’re seeing in the automotive industry when we talk about autonomous vehicles. How do the aircraft interact with the environment with sensors in a city, because you’re going to be flying amongst buildings? You have to be able to sense and avoid other aircraft that are flying. You have to interact with the charging stations that are part of the infrastructure.
It does become a much broader, more complex problem. You have a higher level of connectivity between the different vehicles that are flying around. Then, you need capabilities as simple as being able to track them and enable them to interact with an app on a phone, as people envision something like ridesharing. That is part of how the whole system of systems works. It’s a much more complex problem than we’ve had in the past, and you have to be able to connect all the pieces together and manage them and have them interact properly so that you get the desired performance and usability of the service.
Laurel: Speaking of those types of challenges, as company infrastructures become more like systems of systems to incorporate technologies like AI, artificial intelligence and machine learning, it makes sense perhaps to shift thinking to a systems engineering approach applied to an entire company. What types of technological changes do companies face in integrating systems engineering into an existing architecture?
Dale: There’s always a bit of a cultural challenge, too, as you start to bring in the new systems approach that, sometimes, people just want to jump right in and start designing something. As an engineer, I guess I’ve been guilty of that a few times myself, but you really need to have the systems that help manage your requirements. You can automate the checking of those requirements so that they’re written properly and that they’re decomposing from a system of systems to a product, to the individual subsystems within an aircraft or within a vehicle. So, there is a lot of technology. You have greater interactions between your simulations, the design software that you’re using, and then the tools you’re using to manage the system modeling, but with the higher amount of autonomy that they’re desiring, you start to have more of a system safety influence as well. So, you really need to be able to connect these solutions together so you don’t miss things, so that you can see a complete picture. It’s a lot easier to optimize your products when your software solutions are connected together in a single ecosystem.
That’s the technical side. I mentioned a little bit about the culture and the need for people to change their mindset, to adopt a systems engineering mindset. They no longer are working just on their little piece of the vehicle, but they’re thinking about it in the context of how it influences and interacts with all the other systems on the aircraft—or within the ecosystem, in the case of something like air taxis. You have to look at your processes, you have to look at your people, and you have to look at the technology you’re bringing on board to put together a complete process that empowers the engineers to be more innovative and to think of new solutions.
Laurel: Speaking of that, Nand, what does empowering engineers look like when you’re working on a project?
Nand: From a systems engineering standpoint, allowing them to first define the problem which needs to be solved, then enabling them with the tools and processes required to deliver that, is where empowerment comes into play. There are several levels of technical challenges and solutions, and empowering means enabling them with all those.
Depending on where an individual company or organization is at in its digital transformation journey, those challenges and solutions would be different. From a pure infrastructure or hardware perspective, some will have sufficient hardware installed, which can handle the extensive amount of modeling and computing in their environment. Others will face challenges of making sure there are no silos, to Dale’s point of culture, within the company, and ensuring the information is flowing seamlessly from one end to the other in a digital thread format. Those are the challenges. That’s where it is very important to have an overall plan to have the technology part, as well as the culture and the people side of the business addressed from a talent perspective, in order to deliver a systems engineering approach.
Laurel: A bit more on that, Dale—how do companies look at that kind of challenge, of overcoming the talent gaps and breaking down those information silos? Those are two primary focuses, you could say, of digital transformation across any industry, but specifically for aerospace and defense and automotive. So, it’s a real shift to think of this in a different way.
Dale: Yes. When you start looking at how to address this, you have to go through some amount of training with your people and get them not just to learn the skills, but to adopt the mindset that it takes to be a systems engineer. The other piece of it is looking for the solutions that actually help automate some of those processes.
Sometimes, when you start to break down the barriers, if you think about traditional structural design and structures analysis, like when you’re designing a composite skin panel on an airplane, in the past, the designer would design it in CAD and then hand it off to an analyst to do the stress analysis on the part. Then, they would have to talk back and forth. Now, as you start to bring the tools together and you start to bring the simulation and the design together, you’re now able to start having the same person do both tasks because the tools are easy to use, they’re integrated, and they’re well automated together.
As you extend that into systems engineering, as you try to address the talent gap, there’s only so much you can do with training, but there’s a lot that you can do to help make the tools simpler and easier to use. By making them better integrated, by bringing technologies like AI into it, where you can help automate the generation of different design concepts and the analysis of those concepts using simulation tools, you can extend the capabilities of the system so that it helps empower your engineers.
The companies that are the most successful at adopting systems engineering are doing it because systems engineering and the tools that are being used are becoming almost like the DNA of their engineering organization—everyone is starting to think a bit like a systems engineer, even in their normal job. So, by doing that, you’ve changed your whole organization. You don’t have to rely on a super specialized group of systems engineers to manage that process. Everybody is a stakeholder in that process. The tools and the ecosystem that you use to do systems engineering has a very large role in helping with that problem.
Laurel: Staying on that idea of simulation and artificial intelligence, that is certainly something that needs a lot of data, a lot of engineering to solve these really large problems. How many times do you go to the moon and back when you test out an autonomous vehicle? Hundreds, right? So, you need an enormous amount of data to be able to run the simulation or the models. Could you explain a bit more about how simulation—or even the concept of digital twin, which is creating a digital online environment to mimic what you would be actually building in the field—how does that fit into systems engineering?
Dale: It plays a very big part. It’s almost at the center of it. We often think about systems engineering in the context of requirements, system modeling, and then the verification processes to demonstrate that you’ve satisfied those requirements. That’s a classic closed-loop process of systems engineering, but simulation becomes a very critical tool towards being able to develop the architectures of your product and optimize those products. You can now look at thousands of options. You can run different tests. So, it plays a very big role in helping to define your product upfront.
Then, as you start your verification process, because you have the simulation tools to evaluate the performance of your product in many different configurations, you can identify design changes before you start building a product and before you start testing it. It plays a key role in the definition of the architecture, then the definition of the product, and then finally, the verification of the product. It helps optimize your processes that are being used to develop a new product.
Laurel: Nand, how does that help safety, when you can use simulation or digital twins, or just have more data to make these vehicles more safe?
Nand: Simulation forms the foundation of delivering a digital twin—or systems engineering, in my mind. So, with the simulation in the upfront phases, you can make the right architecture selections, and then move on into the detailed designs. It allows you to explore the space for optimization in delivering that solution. When you combine that with the physical representation of the same simulations and you bring these two things together, that’s how you increase the confidence in your simulation and the physical test results, which is called a CAE test correlation. That helps deliver the systems engineering. So, you could say simulation, digital twin, they go hand in hand in delivering or enabling systems engineering to go from end to end.
Laurel: So, Nand, how does systems engineering help scale product development and/or create this industrial efficiency? What is the return on investment?
Nand: That’s interesting. The industrial efficiency is one of the biggest end deliverables, how you monetize all these investments. I’ll use a couple of examples you asked about earlier. First, how do you deliver a safe vehicle? When you have a lot of simulations done, one of the goals is to reduce the number of physical prototypes built so that you can rely on that simulation. By definition, this is cheaper because you’re not consuming parts and machinery to build those prototypes, and that’s a big thing in the automotive industry. At the same time, you are doing a lot of innovation. There are some things which have not been done in a physical testing environment, so you have to go hand in hand and do some CAE correlation to build confidence. After that point, you’re generating another set of data through simulation. Now, in your next program or the next iteration of the design, you’re a lot more efficient.
Let me take that even further: how does artificial intelligence along with this massive simulation data fit in? There are a lot of cases where you take the simulation data, and through machine learning, you train the algorithms on the outcome of that particular simulation. So, if you’re doing an aerodynamic analysis and looking at a coefficient of drag, it’s intensive from a computational standpoint. Sometimes, those run up to five days to get results. If you’ve trained your algorithms through machine learning and artificial intelligence, you can keep building your database, for given test conditions, on what the results would be. At the end, when you have another new design scenario, you don’t have to do those five-day-long simulations. You put it through those algorithms, and that gives you the results within a matter of minutes. You can see a huge efficiency, both in terms of time it takes to do it and also the computing, which lowers the cost of all those things. That’s how you add on to the return on investments and expand your product development. You scale product development for multiple perspectives by doing more with less, with fewer people because with simulations and all these technologies combined, you can do the same amount of work. Or you could save with the same number of people by pushing through more products. In the automotive industry, you have simultaneously, sometimes, up to 20 programs running, and you can be more efficient.
Laurel: Dale, when we talk about return on investment and aircraft for aerospace defense, we’re talking about investing in a system and hardware that can last for years. An airplane is not replaced within a year. It needs to last a long time. How does ROI affect the way that people think about that with systems engineering?
Dale: That’s a great question. Some of the comments Nand made captured a lot of that very well. I usually think about this in two ways. One is that, when you think about a program, and in aerospace, it’s going through the development program, you’re working with large teams. You look at the budgets that are used for some of these programs, and they might spend 10 million, 20 million, maybe even $100 million a month. As part of that funding, they’re going through the certification process. If you can use simulation to avoid a month or two of delay, that’s a significant amount of money. A lot of times, if you only had a handful of simulation people working on this problem, the ROI can be 10, 20, 30, 40x. It’s a pretty amazing savings when you go through the process, or maybe it’s a pretty amazing cost avoidance.
The other piece of it, that you mentioned, is being able to support these programs over a 50, 60-year product development life cycle. Having the simulation place to be able to understand how the aircraft is performing once it’s out in the field, and by updating the digital twin, the simulation, you’re able to optimize maintenance cycles, which can be a huge cost savings for the operators. Again, the ROI may be in multiples of 10 or 20 on some of that. Sometimes, those costs are hidden, but it’s significant savings.
Then, when you want to upgrade or add new capabilities, because you have that digital twin and you have the simulation in place, you have already done the systems engineering work. It’s easier to integrate and bring new capabilities to the customer. You continue to add value throughout the entire product lifetime. So, the ROI is significant with a lot of these tools and goes beyond the first time you simulate and start designing the vehicle. It pays dividends throughout the entire product life cycle.
Laurel: So, Nand, earlier you mentioned smart cities and that systems engineering approaches could be extended to many different problem types in smart cities. How do you think systems engineering will help further invention and innovation?
Nand: In a smart city, your system has become the city and the vehicle in the city, as an example. Your definition of system has moved from a vehicle to the flow of traffic in the city, how the traffic lights operate in the city, and you can continue to extend that into other aspects of building management, as an example, into the smart city environment. In the autonomous vehicle case, the vehicles will be moving on their own without a driver, so that is part of the city. They have to work with the entire city infrastructure, the entire city traffic systems, the traffic controllers, and the autonomous vehicle. So, it becomes a totally different business case than what we have today. All these things are continuing to allow innovation, both at the technical level as well as at a business model level. As a result of autonomy and autonomous vehicle deployment, new business models are being formed. Whether it’s sharing the vehicle itself or delivering the goods or ride-sharing, that’s what I mean by continuing to innovate around what makes sense and how we can monetize and companies can be profitable.
In terms of the technical side of the business, connectivity is a big piece of it. As consumer trends like people watching Netflix on their phones at home, when they move into their car to go somewhere, they want continuity. They want to continue to watch in the car audio video system. Connectivity allows for more ideas around product development.
The big one in the auto industry is over-the-air updates. So, the whole paradigm shift from having to get a new model of your car every few years to most of the car features being updated through software, allows your hardware to stay the same. You can buy new features without going to a dealership because those features are distributed through software, and they can be delivered over-the-air while the vehicle is parked at your home, or wherever. Again, we’ve expanded the definition of system. The system has become the software being pushed from the author of that software to the end consumer for their products.
Laurel: Dale, how do you feel about innovation and invention with systems engineering?
Dale: Everything we’ve been talking about here today around connected cities and connected cars and connected airplanes and EVTOLs, or air taxis in general, is amazing when you think about the business models we haven’t thought about yet. Something we dream about, at least in aerospace, is like going to the moon—with a system of systems approach and the ability of all the new tools now to be able to look at more options, you might look at a completely different set of how to get to the moon and live on the moon. Instead of a rocket that’s launching, and then you transfer into a lunar lander, and you think about how the Apollo missions were set up, there was a lot of optimization that went into that, but now, you can look at it through the lens of completely different models.
As we start thinking about how we’re using energy around the world and how we’re working toward a more sustainable future, and as smart cities become more and more connected, how are you using energy effectively for your transportation? How are you using it more effectively with your power generation— when the sun gets at the hottest point of the day and you need to have air conditioning, how do you make buildings smarter so that, when there are fewer people in the building, the building can regulate the temperature to save electricity?
There are so many possibilities to think about how we’re using the resources we have and connecting people together better. There are going to be a lot of opportunities as people start to connect all of these devices together, to really become much more aware of our surroundings and how we’re interacting with cities and other people. I’m excited about it.
Laurel: Excellent. Nand and Dale, thank you so much for joining me today on the Business Lab.
Dale: It was great to be here, and I enjoyed the conversation today. Thank you.
Nand: Thank you, again. I enjoyed the conversation as well.
Laurel: That was Nand Kochhar, and Dale Tutt, from Siemens Software, whom I spoke with from Cambridge, Massachusetts, the home of MIT and MIT Technology Review, overlooking the Charles River. That’s it for this episode of Business Lab. I’m your host, Laurel Ruma. I’m the Director of Insights, the custom publishing division of MIT Technology Review. We were founded in 1899 at the Massachusetts Institute of Technology, and you could find us in prints on the web and at events each year around the world. For more information about us and the show, please check out our website at technologyreview.com. This show is available wherever you get your podcasts. If you enjoyed this episode, we hope you’ll take a moment to rate and review us. Business Lab is a production of MIT Technology Review. This episode was produced by Collective Next. Thanks for listening.
This podcast was produced by Insights, the custom content arm of MIT Technology Review. It was not written by MIT Technology Review’s editorial staff.
Recent Comments